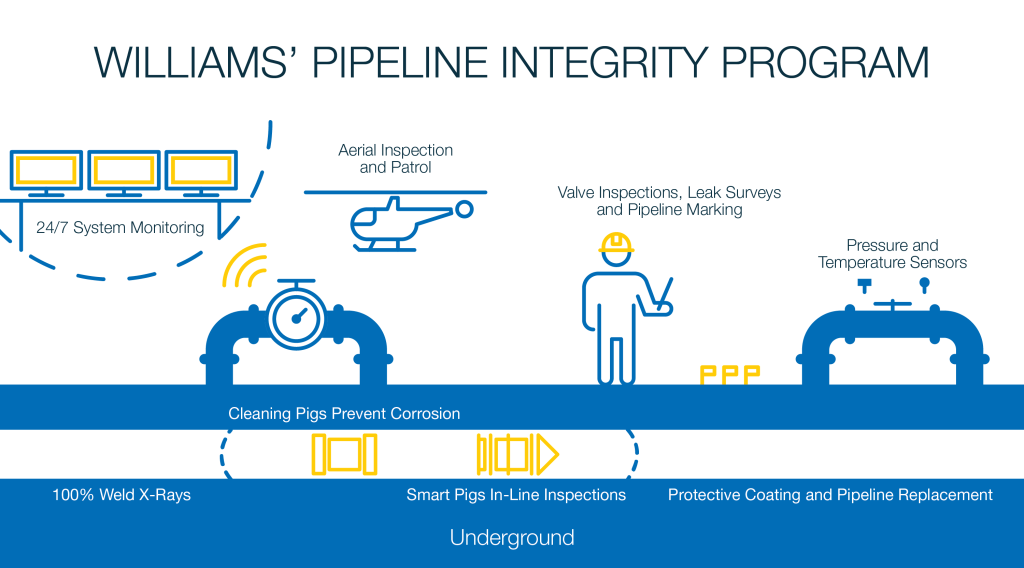
From aerial surveys to ground patrols to advanced robots inside the pipe, Williams uses the latest technology to ensure the safety and reliability of our 33,000 miles of pipelines.
Because pipelines are underground, and out of sight, it’s important to use all available tools to monitor for corrosion, deformation or cracks. And often, the best way to spot a potential problem is with high-tech cameras and sensors inside the pipe through a process called inline inspection.
These devices, often called smart pigs, monitor the health of our pipelines. Inserted into the pipe through a pipeline launcher and propelled by gas or towed by a cable, they travel from one end of a segment to another, monitoring conditions and measuring irregularities as small as a pinhole.
This data is collected by magnetizing the pipe walls and detecting changes in the magnetism or using ultrasonic sound waves, detecting their reflections with electromagnetic acoustic transducers (EMAT).
But what about the robots?
Some Williams pipelines are inspected with robotic inspection crawlers, which self-propel from one end of a segment and back through the same entry point. Guided by an operator outside the line, the articulated crawlers can pass through small-radius bends or tees that bulkier pigs cannot, sending live videos instantaneously.
Why is it called pigging?
It’s not clear how the term pigging came about. Some say pig is an acronym for pipeline inspection gadget while others speculate it reflected the squeaky sound made by some cleaning pigs. Cleaning pigs are used to clear water and debris from pipes.
Today’s cleaning pigs and smart pigs can regulate their speed, which improves data gathering capabilities and reduces impacts to customers.